Manufacturing Processing
- Home
- Manufacturing Processing
Mold Design
After you share the product drawing, our mould engineers team will check and analytics, communicate with you to confirm the mold material, size, requirements and other details for mold, make sure to meet your unique project needs. Then we can confirm the mold positions and cavity count, parting surface. Take the next step, design feed system and etc.

Heat Treatment
Mold heat treatment and surface strengthening are the key technologies, they will affect the mold quality and service life. It has two stages, including pre-heat treatment and final heat treatment. And common methods are normalizing, annealing, quenching, tempering, carburizing, nitrogen and so on. Pick the right method to do the mold heat treatment, according to the different mold materials, to ensure the mold can get the best quality and performance.
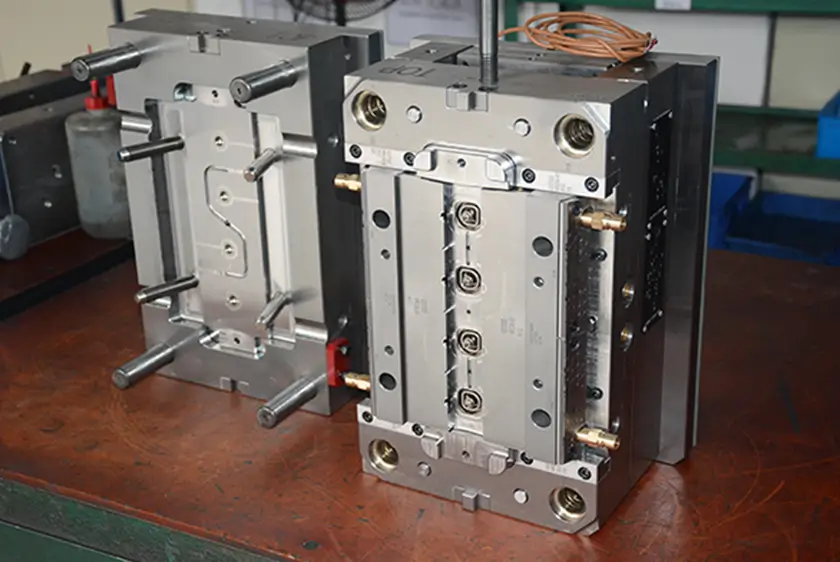
CNC Machining
Compared to normal processing, CNC processing technology is highly automated. Which has better fineness and precision for the product manufacture processing, avoids human error. According to the mold design data, make the 3D mold data, confirm the lathe tool size, tool path mode. Then use the UG to make the CNC program. Finally, our professional machine tool operator will use this data to the processing, including right lathe tool set up, CNC machine program set and so on.

Electrical Discharge Machining
Electrical discharge machining works on the principle of controlled electrical discharges between an electrode and the workpiece submerged in a dielectric fluid. A potential difference is applied between the electrode and the workpiece, creating sparks or electrical discharges. These discharges generate intense heat that melts or vaporizes the material, eroding it incrementally. The dielectric fluid aids in cooling, flushing away debris, and preventing arcing. It is one of the most popular processing methods, and is an important part for mold production. Usually, using it can make product manufacturing for intricate shapes much easier, such as thin ribs, fine details, undercuts, deep cavities and exceptional precision.

Deep Hole Drilling Process
In the mold industry, where precision and complexity are paramount, deep hole drilling has emerged as a critical technique for producing molds that require intricate cooling channels, ejector pin holes, and other specialized features. It is a specialized processing and more complex. If it is unsuitable during the processing, will cause some problems, including workpiece aperture turning large, jam of chip removal and so on.

JIG Grinding
Jig grinding is a type of grinding process that uses a highly accurate and rigidly controlled grinding machine equipped with a specialized jig and grinding wheel. The jig holds the workpiece in a precise position, allowing the grinding wheel to move with high precision along multiple axes. This enables the creation of complex geometries, holes, and surfaces with micron-level accuracy for mold. Jig grinding is a high-precision machining process used in the mold industry to achieve exceptional levels of accuracy and surface finish. It involves the use of specially designed grinding machines and fixtures, known as jigs, to produce intricate features, shapes, and contours on mold components. This process plays an important role in ensuring the precision and quality of molds and dies used in various industries.
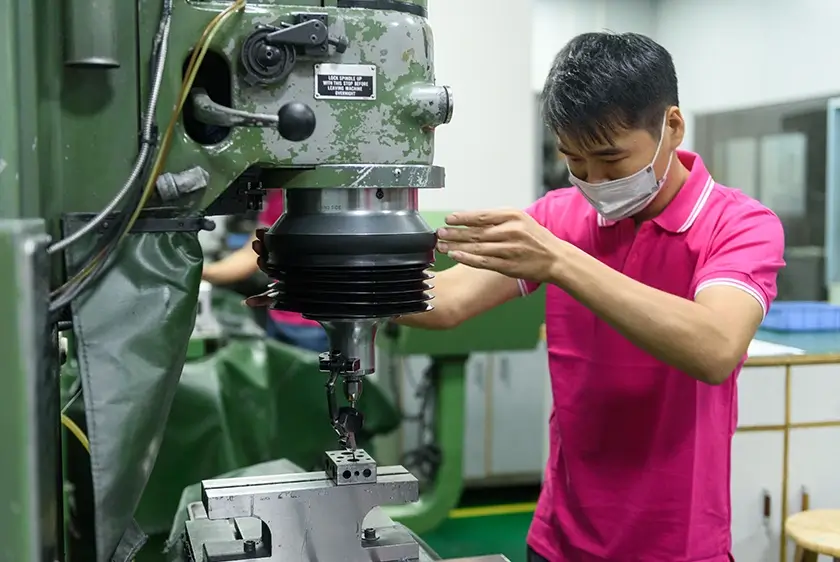